All lubricators have a common goal: Drive oil or grease into the lubrication point, ensuring the smooth operation and prolonged life of machinery, minimal wear and tear, and avoided downtime. Inexpensive and simple to fit, single point lubricators take seconds to install while bringing a wide array of benefits:
- Maximize efficiency
- Save hundreds of maintenance hours
- Increase up-time
- Boost reliability and safety
- Eliminate human error
- Move away from scheduled maintenance
- Provide continuous, uninterrupted lubrication to individual, expensive components
A study involving 12 plants has shown that bearing problems represent approximately 70 percent of all repair events for motors and 30 to 35 percent for pumps and compressors, a number greatly reduced through the application of single point lubrication. Food processing facilities can also avoid cross-contamination, ingress of water and other contaminants with food-grade lubrication applications.
Not all brands of single point lubricators (SPL) are identical. Though they get the same results through their individual ways of applying lubrication, there are also differences in the way they operate as well as varying bearing size, load, environment, temperature, type and speed, thus specifying a use for different applications and conditions.
Types of Powered Lubricators
There are basically three types of powered lubricators, classified by how they push the grease: gas, electrochemical , and electromechanical. All three automatically inject grease but have different aspects as to their use and why.
The same grease types can be supplied for each of these products. Cost and feedback do play a part in the selection as well as the amount of bearings and their criticality.
1.) Gas Powered Lubricators
The gas powered units are actuated by mixing an electrolyte and zinc pellet to form a gas. The gas expands against a plunger that pushes the grease out of the unit at 45 PSI. They have a 3-6-9-12 month dispensing range that requires a different concentration of zinc. However, they are temperature dependent.
That is, when it is 0° they will push harder for less grease; whereas, when it is 90° they will work less to lube the bearing. Some of the canisters are made of metal so you will not know if the unit is operating properly or injecting the grease. These cost the least out of the 3 and are a throw away.
2.) Electrochemical Lubricators
Electrochemical units use a battery, microprocessor and an electrolyte to create a gas that pushes the grease. The processor tells the battery to excite the electrolyte to create a gas. The processor compensates for low temperature.
When it is 10° the processor senses it and adjusts the unit accordingly. The unit dispenses the same amount of lubrication no matter what the outside temperature is. Some units have dip switches or jumpers that can be set for each of the different month settings. These units can be paused or turned off if the equipment is going to be out serviced for a period of time.
3.) Electromechanical Lubricators
All electromechanical lubricators have a battery, pressure source, programmable controller (LED) , and grease pack. The LED controls a motor that pushes the grease. The type of motor dictates the amount of pressure the unit is capable of. This is important depending on how far the bearing tap is from the unit .
They have replaceable batteries and grease packs so purchasing the complete unit is not necessary, making it economical after the initial purchase is made. The most important feature is the feed back if the bearing does not accept the lubrication which separates it from the other two types of lubricators.
If the bearing or lube line is clogged and the unit can not push the grease, a fault occurs. There will be a flashing indication on the LED. This is very important for critical bearing. If and when this occurs some units have a memory that can be checked to see when the last lube event took place.
The units that can produce pressure of 400 PSI plus can do multiple bearings using a divider valve. They can do 1 to 8 bearings because they lube only one bearing at a time. Keeping in mind the shorter the lube lines the better.
Smart Factories and IOT
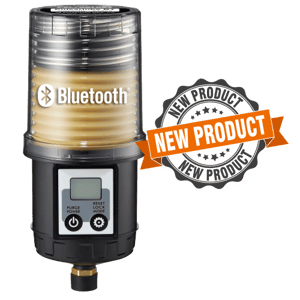
With advanced, computer-integrated manufacturing, products are now available to accommodate the data processing, industrial connectivity, and advanced robotics of these Smart Factories. The Pulsarlube BT is a brand new, Bluetooth-enabled automatic lubricator that can be monitored and controlled from an app on a mobile device.
This Bluetooth-enabled, automatic electromechanical lubricator makes finding lubricators, monitoring status, and changing settings very simple and convenient.
- Conveniently control and monitor lubricators using the Pulsarlube mobile app
- Easy to use app interface
- Various grease pouch capacities and lubricant types available
- Straightforward installation and operation
- Remotely monitor lubricator status in hazardous and inaccessible work areas
- Monitor operational status of all paired lubricators by using the integrated database
To survey your current application or for additional information, please contact LubriSource to discuss your application.