Keeping your lubrication system as free of water as possible is essential to an effective maintenance program. Water is a costly and destructive contaminant that results in premature component wear and accelerated lubricant degradation. Following best practices for storage, along with installing adequate moisture prevention and removal equipment, ensures the water saturation level in your system remains low.
The first step to moisture contamination prevention is understanding and recognizing the states in which water is present in your system.
- Dissolved water is dispersed throughout oil as uniformly distributed molecules. Because there are no obvious signs of its presence, this mixture can result in high concentrations of moisture that go unnoticed until a critical point is reached. Depending on its temperature and age, oil can hold up to 200 to 600 ppm of dissolved water before reaching the full saturation level.
- When the moisture saturation level peaks, water becomes emulsified. The water molecules are then suspended in the lubricant, often causing milkiness or haziness and foaming.
- If condensation in the system continues or additional moisture is introduced, free-state water results. The oil and water separate, and free water accumulates in the bottoms of tanks, reservoirs, and sumps.
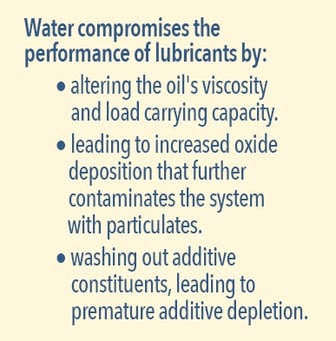
Free and emulsified water are the most destructive to machinery and lubricants. Water compromises the performance of lubricants through altering the oil's viscosity and load carrying capacity. Oil oxidation rates also can change, leading to increased oxide deposition that further contaminates the system with particulates. Additionally, excess moisture washes out additive constituents, leading to premature additive depletion.
The resulting damages to internal components can include:
- Surface corrosion and increased brittleness of components
- Pitting, spalling, and cracking of metals
- Accelerated bearing deterioration
- Erosive wear due to flash-vaporization oil
It is difficult to completely eliminate water from your lubrication system, therefore, the goal is to keep the moisture level as low as possible. Contamination prevention begins with resolving condensation, humidity, and ingress issues. Environmental moisture, leaking seals and covers, and inappropriate or compromised storage containers are all avenues of moisture contamination. Common best practices for lubricant storage are:
- Adequate protection of storage drums and tanks in an outdoor environment
- Protection of indoor containers from cleaning and processing sprays
- Installation of desiccant filters in humid storage areas
Adequate monitoring of water saturation levels is essential in avoiding unseen interior component wear that can lead to sudden, unexpected equipment failure. Three common water measuring methods are:
Crackle testing – A means of roughly determining water saturation level by correlating the amount of bubbling of a drop of oil when it's applied to a hot plate. This method does not offer a precise measurement but is a quick test for an on-the-spot assessment.
Capacitive water sensor– A real-time measurement of water saturation levels via analyzing capacitance variation of a substrate, as influenced by the transmission of water through an adjacent dielectric layer. This method is precise and can also be utilized as a water saturation control device.
Titration or Karl Fischer moisture test – A measurement of absolute water content that gives the most precise assessment. However, this method is not appropriate for time sensitive applications as there is a longer wait time for saturation level results.
When prevention of water contamination of lubricants isn't enough, there are several effective options available for removing moisture from your system.
- Absorbent filter elements - Often a cellulose-based layer in a general filtration system, this method is an inexpensive way to remove emulsified and free water. However, its usefulness is limited by its minimal volume capacity, making it most suitable for small systems, units, and portable carts.
- Desiccant breather - This method is a contamination filtration system that utilizes a layer for water absorption, commonly, silica gel. These filters are available in different sizes and can be stationary components fitted to equipment and storage tanks. Additionally, the desiccant-type can be specified according to the lubricant being filtered, and dyes that indicate filter saturation level are often included.
- Gravity draining - This method of water removal only works for lubricants that aren't formulated for water suspension. It's a low-cost solution for removing, via gravity and a release valve, free water that has settled in the bottom of tanks and reservoirs.
- Centrifugal removal – This method is effective for low specific gravity and low viscosity oils. The centrifuge separates emulsified and free water from oil by spinning the lubricant at high speeds. This is a somewhat expensive solution, though, it has the benefit of high volume processing and removal of additional particulate contaminants.
- Vacuum dehydration - This option has the advantage of removing moisture in the system to very minimal levels. The method involves lowering of pressure as the lubricant passes over a series of heated plates within the unit, so that the lubricant boils at a lower temperature, allowing water to vaporize without degrading the oil. Due to the high cost and low flow rate of this system, it is commonly rented as-needed for lubricant decontamination and restoration purposes.
Preventing water contamination of lubricants extends the life of oils, additives, and machinery. Regular monitoring and testing of moisture levels can reduce the frequency of equipment failure and downtime. When water saturation levels peak, removing that moisture from your system as soon as possible is critical for maintaining efficient production.
Reduce your facility's operating expenses and make your lubrication maintenance job easier by consulting with us for effective water contamination prevention and removal strategies.